
PUMPA - SMART LEARNING
எங்கள் ஆசிரியர்களுடன் 1-ஆன்-1 ஆலோசனை நேரத்தைப் பெறுங்கள். டாப்பர் ஆவதற்கு நாங்கள் பயிற்சி அளிப்போம்
Book Free DemoMetallurgy of Copper:
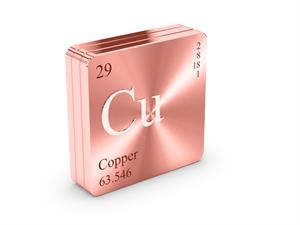
Copper symbol, atomic number and mass.
Occurrence: The Romans called it Cuprum because they obtained it from the island of Cyprus. Copper received in the native state as well as the combined state.
Copper production in India is only about 2% of global copper production; India's major copper mines are located on the Kathri Copper Belt in Rajasthan.
The primary ores of copper are as follows:
Ores of copper | Formula |
Copper pyrites | CuFeS_2 |
Cuprite or ruby copper | Cu_2O |
Copper glance | Cu_2S |
The primary ore of copper is copper pyrite. It gives nearly 76% of the global production of copper.
Copper pyrite or Chalcopyrite is the most common copper ore and a copper iron sulfide mineral. It has the chemical formula CuFeS_2 and crystallizes in the tetragonal system. It has a brassy to golden yellow colour and a hardness of 3.5 to 4 on the Mohs scale. Its streak is distinguished as green-tinged black.
The following steps are involved in copper extraction from copper pyrites:
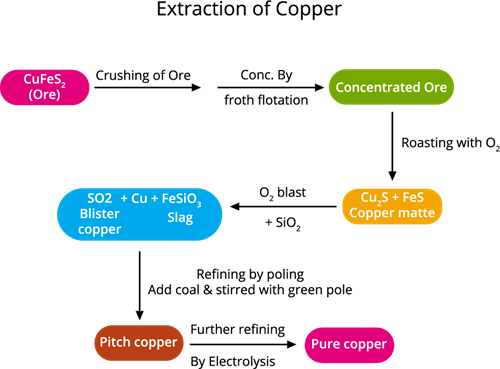
Copper extraction flowchart
Step 1. The concentration of ore: (removing impurities from the ore)
The ore is crushed, then the froth floatation process is used to concentrate it.
Step 2. Roasting:During this process, the moisture and volatile impurities are removed. The concentrated ore is roasted over the air. Sulphur, phosphorus, arsenic and antimony are removed as oxides.
Roasting is the method of heating a sulfide ore to a high temperature in the presence of air.
Copper pyrite is partly converted into copper and iron sulphides.
2CuFeS_2 + O_2 → Cu_2S + 2FeS + SO_2↑
Step 4. Smelting:
Smelting is a type of extractive process (using heat and a chemical reducing agent) used to extract (decompose) a metal from its ore.
The roasted ore is combined with powdered coke, sand and heated in a blast furnace to produce matte (Cu_2S + FeS) and slag. The slag is disposed as waste.
Step 5. Bessemerisation:
Bessemerisation (the final stage of smelting) is when the air is blown into the molten copper mat deposited in a Bessemer converter.
The molten matte is transported to the Bessemer converter to produce blister copper. Ferrous sulphide from matte is oxidised to ferrous oxide, which is removed as slag with silica.
2FeS + 3O_2 → 2FeO + 2SO_2↑
FeO + SiO_2 → FeSiO_3 (slag)
FeO + SiO_2 → FeSiO_3 (slag)
(Iron silicate)
2Cu_2S + 3O_2 → 2Cu_2O + 2SO_2↑
2Cu_2O + Cu_2S → 6Cu + SO_2↑
2Cu_2S + 3O_2 → 2Cu_2O + 2SO_2↑
2Cu_2O + Cu_2S → 6Cu + SO_2↑
(Blister copper)
Step 6. Refining: (Refining is a process of purifying an impure metal)
Blister copper includes 98% of pure copper and 2% of impurities and is purified by electrolytic refining. This method is used to get high purity metal. We use electrolytic refining copper.
Electrolytic refining is the method of refining a metal (mainly copper) by electrolysis. A large piece of impure copper is used as the anode with a thin strip of pure copper as the cathode. Copper(II) sulphate solution is the electrolyte. Copper dissolves at the anode: (Cu → Cu_2 + 2^e) and is deposited at the cathode. The final result is the transfer of pure copper from anode to cathode. Gold and silver in the impure copper form a anode sludge at the bottom of the cell, which is recovered.
Cathode: A thin pure copper plate.
Anode: A block of impure copper metal.
Electrolyte: Sulphuric acid is used to acidify copper sulphate solution.
When a current is passed in the electrolytic solution, the pure copper is deposited at the cathode. Impurities settle to the bottom of the anode as sludge, known as anode mud.