
PUMPA - SMART LEARNING
எங்கள் ஆசிரியர்களுடன் 1-ஆன்-1 ஆலோசனை நேரத்தைப் பெறுங்கள். டாப்பர் ஆவதற்கு நாங்கள் பயிற்சி அளிப்போம்
Book Free Demo(iii). Smelting (in a Blast Furnace):
Smelting is a type of extractive process (using heat and a chemical reducing agent) used to extract (decompose) a metal from its ore.
Blast furnaces are large, intricate systems built with a combination of off-the-shelf and custom-made components. The blast furnace's most essential components are the furnace shell, the furnace's internal refractory lining, and the crucible-like hearth. Most of the stand-alone equipment, such as motors, burners, etc., is associated with raw material assembly and transport, Hot metal and slag transfer, Off-gas cleaning, and Hot-blast stoves.
The charge, made of roasted ore, coke, and limestone in the proportions of 8:4:1, is melted in a blast furnace by introducing it through the top hopper arrangement.
There are three essential regions in the furnace:
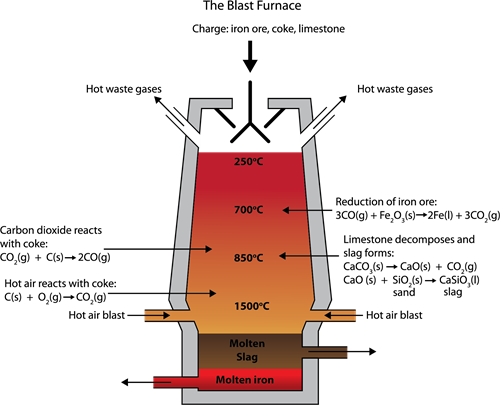
Blast Furnace Equipment
(a). The Lower Region (Combustion Zone):
In this region, the temperature has reached 1500°C; Here, coke burns with oxygen to form CO_2 when the charge (solid iron ore, coke, and limestone) comes in contact with a hot blast of air.
It is an exothermic reaction because heat is released.
(b) The Middle Region (Fusion Zone):
In this region, the temperature is around 1000°C, here CO_2 is reduced to CO.
Limestone decomposes to calcium oxide and CO_2.
The above two reactions are endothermic due to the absorption of heat.
Calcium oxide bind with silica to form calcium silicate slag.
(c). The Upper Region (Reduction Zone):
In this region, the temperature is 400°C, here carbon monoxide reduces ferric oxide to form a relatively pure spongy iron.
After the removal of slag, the molten iron is collected at the bottom of the furnace.
The iron thus formed is called pig iron. It is remelted and cast into different moulds. This iron is called cast iron.